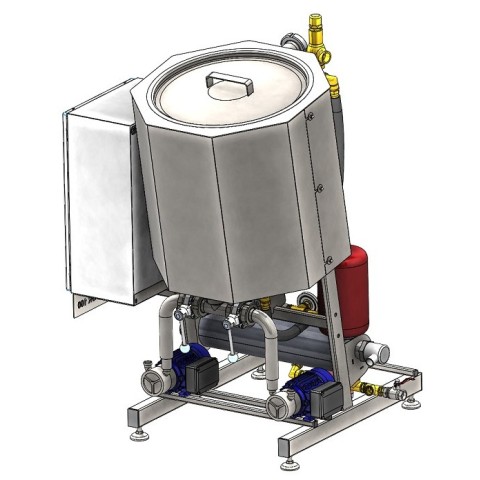
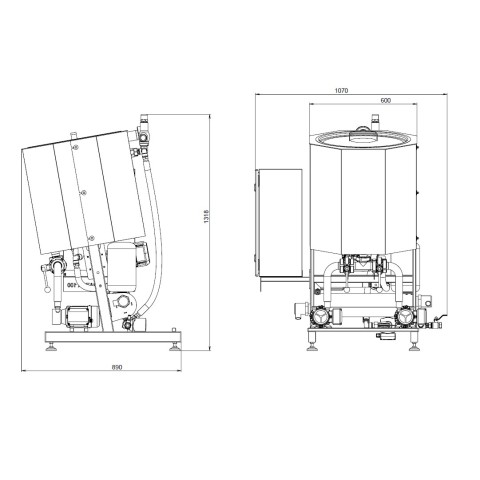


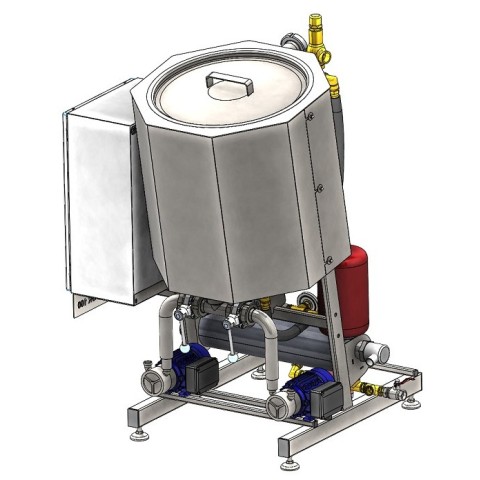
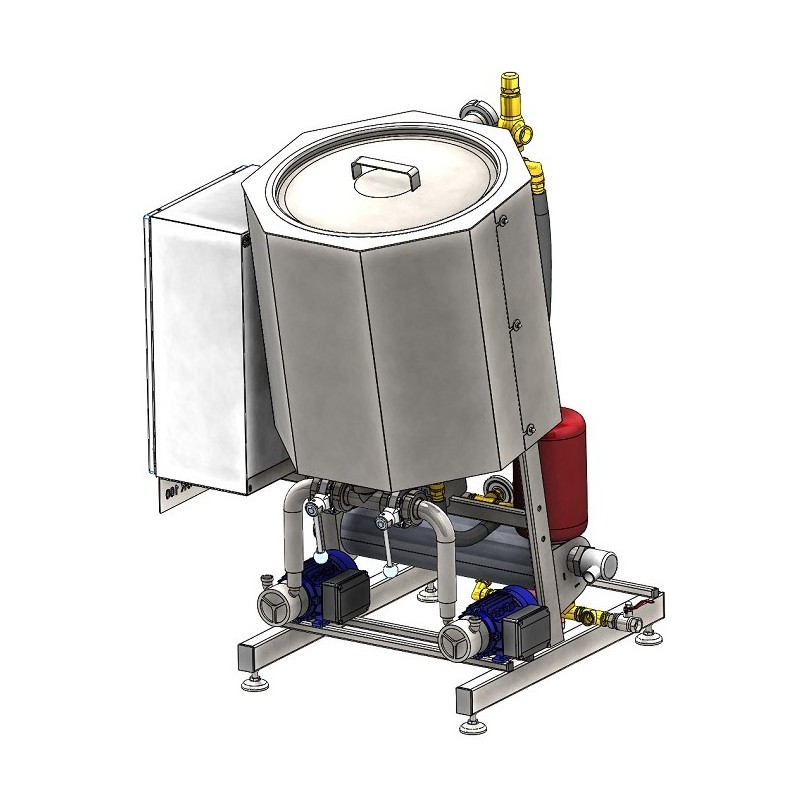
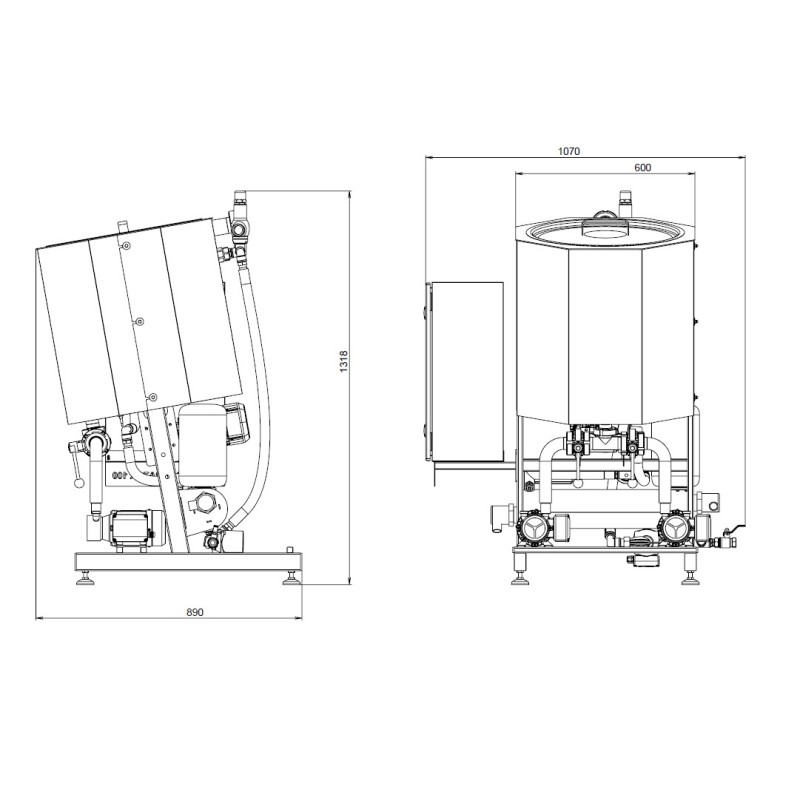
Tank with a mixer and jacket for the thermal carrier
The atmospheric tank with an inclined design is used for mixing, stirring, and dissolving various products. By supplying a thermal carrier to the unit’s jacket (duplicator) from an external source, thermal processing such as heating or cooling can occur (i.e. heating or cooling from an external coolant source with an inlet pressure of up to 0.5 bar). These units are widely utilized in the food and cosmetic industries.
- Inclined design: 50% more efficient mixing
- Due to the inclination angle of the working tank, rapid and complete (100%) emptying is achieved.
- Efficient heat transfer through the heating/cooling jacket
- No dead zones during mixing!
- Modular system with a wide range of additional options
Atmospheric mixers with a frame stirrer and a jacket for the heat transfer medium (for heating or cooling) are suitable for use in the food, cosmetic, chemical, and many other industries, as they allow a wide range of processes to be performed, including:
|
|
|
|
|
|
|
|
|
Atmospheric tanks with a stirrer and a heating/cooling jacket are suitable for the production of such products as:
|
|
|
|
|
|
|
|
|
|
|
|
And much more!
Advantages:
- Hygienic design: virtually eliminates product contamination after washing, as there are no blind zones inside the reactor.
- No dead corners due to gravity mixing, the product flows to the lowest point, from where it is raised by the mixer and mixed into the total mass. Gravity mixing is 50% more efficient than usual. It allows intensive mixing, and the mixing of thick and viscous products.
- The inclined design of the unit also helps to quickly unload the product while the mixing device is on.
- The unit can be equipped with various types of frame mixing devices.
- The heating/cooling jacket up to 0.5 bar allows the use of steam or hot water as a heat carrier for heating, and if cooling is necessary, cold water or glycol can be supplied to the jacket.
- A professional stainless steel temperature sensor is installed in the bottom of the working tank, certified for use in contact with food products.
- Robust design, all components are supplied only from European manufacturers. All connections, joints, fittings are made only out of stainless steel AISI 304 and 316L, connections - fittings used in dairy processing from German manufacturers such as AWH. All connections have high-temperature Viton seals. The tanks are resistant to acids, alkalis and high temperatures.
- The internal surfaces are polished to RA ≤ 1.6 µm. Mirror internal surfaces (for the pharmaceutical industry) can be ordered as an option.
- Convenient maintenance due to the inclined design even with large installation volumes. Space saving in production facilities – compact, high-performance tanks.
Basic version:
The unit is equipped with a frame stirrer with a professional industrial three-phase gear motor as standard. The reactor has a two-layer casing with a heating/cooling jacket (up to 0.5 Bar), thermal insulation and an external decorative casing can be installed as an option. In the basic version, the internal surfaces of the mixers is polished, the welds are cleaned and etched. Optionally, the internal surface of the mixer can be polished to Ra <0.4 µm. Hot water or steam can be used as a heat carrier. The mixer is equipped with a professional stainless steel temperature sensor in the product at the bottom of the tank.
Options:
- Various types of mixing devices
- Scrapers for the agitator
- CIP heads
- Hot water supply source
- Steam generator
- Ice water stations
- Thermal insulation with an external decorative casing
- And much more...
The images contain models with the maximum configuration, and are posted for informational purposes. Actual installations may differ from those shown.
- Material: Stainless steel
- Principle of operation: Batch mode
- Type of the equipment: Individual machine
- Country of origin: Slovakia
- Working volume: 100l/ 200l/ 300l/ 450l/ 600l/ 900l
The cooling tank is designed for storing milk and other beverages.
- Material: Stainless steel
- Principle of operation: Batch mode
- Country of origin: EU
The professional cooking vat is designed for dairy products processing. The machine can be used by farms and small dairy factories.
- Material: Stainless steel
- Heating power, kW: 24
- Volume: 150l/ 300l/ 500l
The vacuum crystallizer-cooler is specifically designed for sweetened condensed milk. Crystallization with cooling is one of the most important stages in the production of condensed milk according to GOST and is necessary before dosing and packing the finished product.
- After crystallization, condensed milk has a delicate structure with small crystals
- Condensed milk has a homogeneous shape and attractive consumer properties
- The shelf life of condensed milk is extended without changing the quality of the product
- Material: Stainless steel
- Principle of operation: Batch mode
- Country of origin: Slovakia
- Volume: 100l/ 300l
- Voltage: 380-400V
- Max vacuum: -0,8 Bar
The vacuum cooking and concentration unit is designed for concentrating products at low temperatures (about 60 degrees) in a reactor with a discharged environment to preserve the color, nutritional value and useful natural substances in present in food products. Evaporation and concentration units are often used when cooking jams, sauces, as well as fruit or vegetable concentrates. The vacuum concentrator allows you to boil and concentrate heat-sensitive products without damaging or destroying their structure or proteins, such as milk.
- Inclined design - allows for gravity mixing, which is 40% more efficient than usual
- Quick and 100% emptying of the tank thanks to the inclined design with the mixer on
- Heating/cooling jacket (duplicator) for the working tank and bottom
- High hygiene standard - the output valve is located at the lowest hydraulic point of the reactor
- Material: Stainless steel
- Principle of operation: Batch mode
- Country of origin: Slovakia
- Volume: 300l/ 500l/ 875l
This equipment is often used for temporary storage and transportation of liquid products, equipped with a specially shaped stirrer and heating / cooling "jacket".
- Material: Stainless steel
- Engine power, kW: 0,25
- Principle of operation: Batch mode
- Voltage: 380-400V
A vacuum evaporator is a device used to evaporate liquids at lower temperatures by creating a vacuum environment, which reduces the boiling point of the liquid and enables efficient evaporation without thermal degradation of sensitive materials. Working volume up to, l: 1900 l.
- Heating: Electricity
- Material: Stainless steel
- Heating power, kW: 30
- Principle of operation: Batch mode
- Country of origin: Slovakia
- Working volume: up to 1900 l
A vacuum distillation system is used for controlled separation of liquids based on the evaporation of the liquid and subsequent condensation of its vapors.
- Material: Stainless steel
- Country of origin: Slovakia
- Volume: 5l
The laboratory vacuum cutter mixer is designed for uniform grinding, emulsifying and mixing of food, cosmetic and pharmaceutical products, chemical mixtures with the addition of oil, dyes, concentrates or liquid flavors.
- Material: Stainless steel
- Principle of operation: Batch mode
- Country of origin: Slovakia
The price is indicated with a semi-automatic control panel
The vacuum cooking kettle is designed for use in public catering establishments (restaurants, hotels, catering companies) and small manufacturing businesses. This equipment enables boiling, blanching, frying, evaporation, pasteurization, mixing or stirring.
- A unique multifunctional device
- Possibility to cook/fry under atmospheric or vacuum conditions
- Laboratory version of a Vacuum Fryer
- Built-in condensation and secondary steam removal system
- Intense electric heating
- Sectional basket with a lid
- Built-in system for separating and removing excess liquid from the product
- Heating: Electricity
- Material: Stainless steel
- Heating power, kW: 5
- Volume: 20l
- Oil volume: 8l
- Voltage: 380-400V
- Max vacuum: -0,8 Bar
This open tank is intended for washing the juice tanks. Kapacity 250L. For more information, send us a request.Â
- Material: Stainless steel
- Volume: 250l/
Model VMG S is an effective and reliable vacuum homogenizing unit designed to produce a wide range of liquid, pastry and viscous products with different requirements for the production conditions.
Tilting bratt pans with mixer are frying the product with continuous stirring. Designed for catering industry, school kitchens, restaurants and food industry. Variants of heating systems: direct electric and direct gas. Capacity: 150, 200 or 300l.
- Material: Stainless steel
- Engine power, kW: 0,75
- Heating power, kW: 42
- Principle of operation: Batch mode
- Type of the equipment: Individual machine
- Country of origin: EU
- Volume: 150l/ 200l/ 300l
- Voltage: 380-400V
The sorption filter 3000l refers to non-pressure equipment of periodic action for filtering liquids using bulk filtering agents and different sorbents.
- Material: Stainless steel
- Principle of operation: Batch mode
- Type of the equipment: Individual machine
- Country of origin: Slovakia
- Volume: 3000
A Vacuum cooker is a versatile device used in culinary settings to cook food under vacuum conditions, enhancing flavors and textures while also reducing cooking times.
We offer various different cookers.
- Material: Stainless steel
- Principle of operation: Batch mode
- Country of origin: Slovakia
- Volume: 100l
- Voltage: 380-400V
Working volume: 1000 l =Â Honey dose: 1500 kg
Working volume: 2000 l =Â Honey dose: 3000 kg
The price depends on the chosen option.Â
- Productivity: do 3000 kg
- Material: Stainless steel
- Country of origin: Slovakia
- Working volume: 2000 l
- Geometric volume: 4000 l
- Dimensions, mm: 4300x2760x2450
A circulation-type vacuum evaporator refers to a combined version of an evaporator that also takes advantage of other types to improve evaporation efficiency particularly by reducing concentration time and when processing heat-sensitive products such as milk.
- The external circulation circuit with heating intensifies the cyclic evaporation process.
- The forced circulation system ensures a decrease in the risk of localized product overheating.
- The condenser enables a deep vacuum and maintains a low evaporation temperature.
- Utilizing a mixing device with a spray system facilitates product evaporation in a thin layer, mimicking a film-type evaporator.
- Heating: Steam
- Material: Stainless steel
- Operation mode: Semi-automatic
- Country of origin: Slovakia
- Total power, kW: 2,4
- Voltage: 380-400V
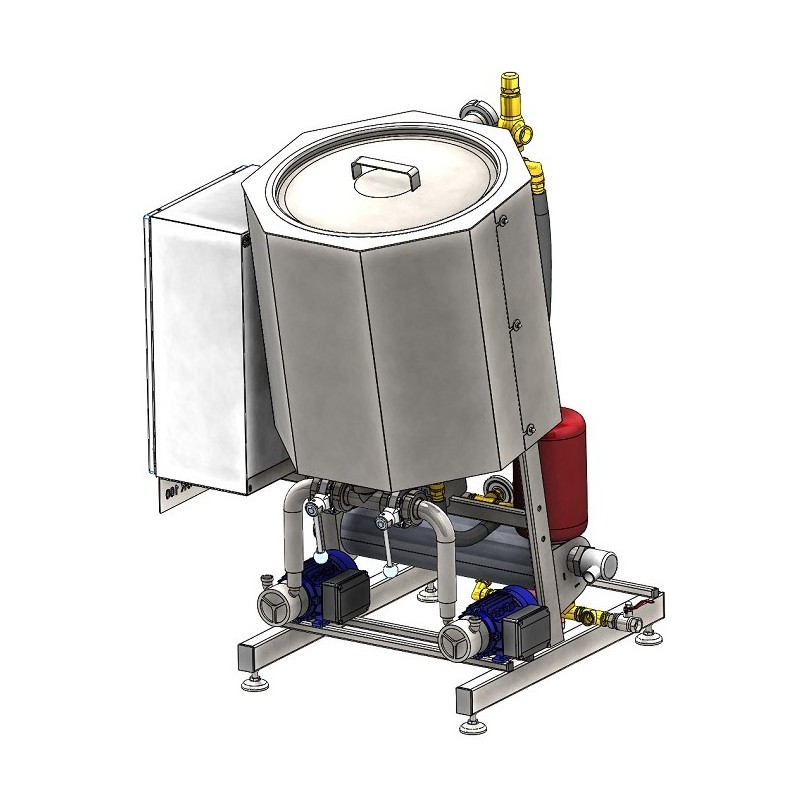
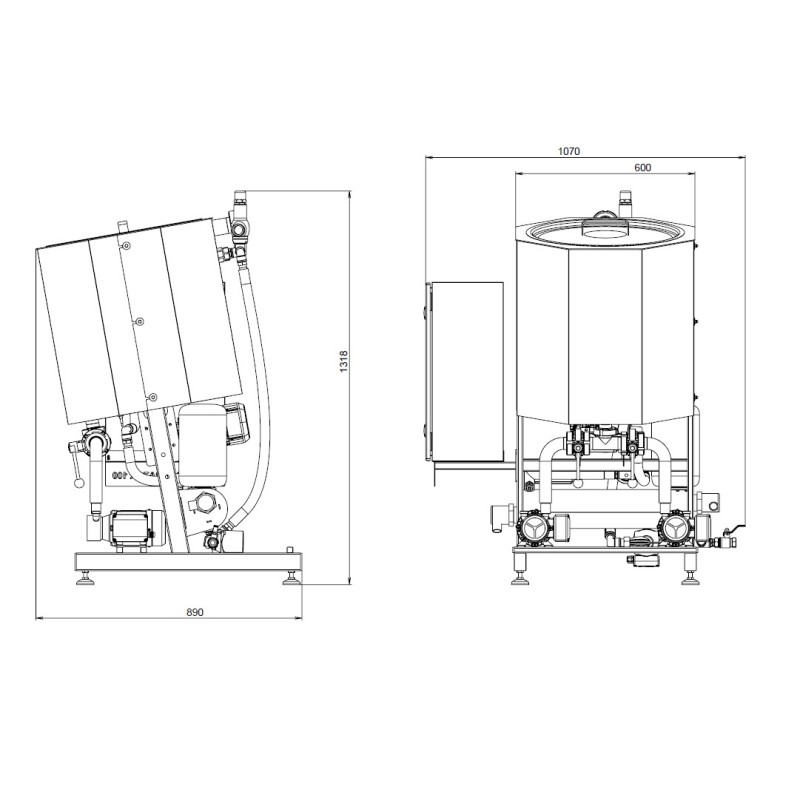