Wetting and washing grain is a process performed to prepare it for milling.
When wetting is carried out, psychobiological processes changes take place in the grain, which simplifies the separation of the skins from the grain with slight losses of endosperm( inner part of the seed); during washing, the surface of the grain is cleaned, heavy and light impurities, peels and microorganisms are removed.
In combined washing devices, water is used to separate impurities that are difficult to remove in a dry grain cleaning process. The basis of hydro separation is the determined difference between the rate of grain and impurities in the water. decline.
The construction of the equipment was constructed in cooperation with the leading engineers of bakery companies. They consider and corrected all the disadvantages of the grain washers that were still on the market. The grain at the outlet of the device has a minimum level of moisture because the grain practically does not have time to get wet. Usually, no drying is required. The centrifugal device is located at the top of the drum.
Technical features
- Drive screw conveyors on a separate frame
- Sand and stone removal system
- Screw conveyors for product and sand
- Ejection chamber
- The system for dewatering and removal of foam, dirty water
- Water level regulator
- Filter
- Ejectors with pipelines supplying a water product mixture to the separation column
- Rotor - stator separation column
- Separation column drive
- Separated water outlet system for circulation
- Centrifugal product discharge system
- Adjustable feet
- Shut off valves.
Principle of operation
The grain is fed into screw conveyors in different places, depending on the presence and amount of unwanted impurities - such as small stones, sand, metal particles. If there is a lot of such impurities, the grain is placed in the starting section. If no such impurities are present, the grain can be placed directly in the ejector zone, which guarantees the best indicators of grain dryness. The skins, light dirt, and dust remain on the surface and partially dissolve.
The peels are caught by a filter that is easy to clean without having to stop the machine. The mud creates a foam that effectively gets rid of the defoaming system, which is flexibly adjusted to achieve the optimal result.
The grain at the exit is
- Clean
- Dry
- Undamaged
The approximate capacity of the plant is about 1500 kg / h, but with considerable contamination, productivity decreases
Technical features and benefits:
- Without shaft seals, which often loosen and need to be replaced, they cause leaks.
- Adjustable tools for highly efficient grain processing of any degree of contamination.
- Effective de-foaming system
- Adjustable water level
- The device is equipped with filter
- An optional circulating water recirculation system is available, which provides very significant savings in operation.
- The device is equipped with a highly efficient washing separation column system.
- The construction is made entirely of stainless steel, which guarantees long life.
- And many other improvements
- Productivity: 1500 kg/h/
- Material: Stainless steel
- Principle of operation: Continuous mode
- Type of the equipment: Individual machine
You might also like
The machine is used for brushing, cleaning as well as prewashing various root vegetables.
- Material: Stainless steel
- Engine power, kW: 2,2
The NORMIT drum mixers are designed for thorough mixing for products such as combined feed for animals, infant formulas, baby food, food concentrates and additives, sports supplements and nutrients, coffee, tea, pharmaceuticals and chemical products.
- Material: Stainless steel
- Principle of operation: Batch mode
- Volume: 50l/ 100l/ 150l/ 200l/ 500l
Fruit washer is designed for washing and cleaning products such as fruit or vegetables before processing, especially apples.
If you're looking for any other fruit and vegetable washers, send us a request.Â
- Material: Stainless steel
- Principle of operation: Continuous mode
The washer-auger-mill machine is designed for washing, transporting and milling whole fruit or vegetable before further processing.
Price depends on your product and the production capacity. For more information, send us a request.
- Productivity: 3000 kg/h
- Material: Stainless steel
- Principle of operation: Continuous mode
This machine is suitable for washing fresh fruits and vegetables. We offer 2 different capacities.
- Productivity: 1000 kg/h/ 3000 kg/h
- Material: Stainless steel
- Engine power, kW: 0,55/ 0,75
- Principle of operation: Continuous mode
- Voltage: 380-400V
The brush washer/scraper is an industrial device for washing and scraping root vegetables depending on the degree of contamination.
- Productivity: 300 kg/h
- Material: Stainless steel
- Engine power, kW: 1
- Voltage: 230 V/ 380-400V
Cleaning-In-Place - Machine for cleaning and disinfection of vessels and pipelines in breweries and other food processing plants with four tanks.
- Heating: Electricity Steam
- Material: Stainless steel
- Voltage: 380-400V
Dimensions: 2000x1230x1600
Volume: 150 l
Performance: up to 3000 kg/hour
Price on request.
- Productivity: do 3000 kg
- Material: Stainless steel
- Principle of operation: Continuous mode
- Volume: 150l
- Voltage: 380-400V
- Dimensions, mm: 2000x1230x1600
The container washer for canned food is a specialized washing system designed to thoroughly clean containers used for canning food products, ensuring hygiene and sanitation standards are met within your food processing facility.
- Material: Stainless steel
- Principle of operation: Continuous mode
- Country of origin: Slovakia
The washer-elevator-mill machine is designed for washing, transporting and milling whole fruit or vegetable before further processing.
- Productivity: 1000 kg/h/
- Material: Stainless steel
- Principle of operation: Continuous mode
CIP station CIP-101 With a usable capacity of 1×100 liters, it is used for cleaning, sanitizing and sterilizing vessels and pipes in a brewery. This type of CIP station is recommended for cleaning and sanitizing tanks from 0 to 4000 liters.
- Material: Stainless steel
- Country of origin: EU
The washer with external loading conveyor UNI M is specifically designed for the efficient and high-performance washing of vegetables, potatoes, and fruits, using gentle exposure to water to ensure thorough cleaning without harming the product.
- Material: Stainless steel
The washer-auger-mill machine is designed for washing, transporting and milling whole fruit or vegetable before further processing.
Price depends on your product and the production capacity. For more information, send us a request.
- Productivity: 3000 kg/h
- Material: Stainless steel
- Principle of operation: Continuous mode
This machine is suitable for washing fresh fruits and vegetables. We offer 2 different capacities.
- Productivity: 1000 kg/h/ 3000 kg/h
- Material: Stainless steel
- Engine power, kW: 0,55/ 0,75
- Principle of operation: Continuous mode
- Voltage: 380-400V
We offer different types of washing equipment for various different fruits and vegetables.
- Productivity: 1500 kg/h
- Material: Stainless steel
- Engine power, kW: 3
- Weight: 200
- Productivity: 300 kg/h
- Material: Stainless steel
- Principle of operation: Continuous mode
- Type of the equipment: Individual machine
The CEP washing machine is a mobile cleaning station designed to efficiently clean various containers, including mixers and boilers, suitable for use in the food, chemical, and pharmaceutical industries.
- Material: Stainless steel
- Principle of operation: Batch mode
- Country of origin: Slovakia
- Weight: 85
We offer a wide range of washing equipment tailored to diverse food products, ensuring optimal cleanliness and preparing your fruits and vegetables for the next processing stage.
- Productivity: 2000 kg/h 3000 kg/h
- Material: Stainless steel
- Principle of operation: Continuous mode
- Country of origin: EU
CIP-302: Cleaning-In-Place - Machine for cleaning and disinfection of vessels and pipelines in breweries and other food processing plants with two tanks of 300 liters.
- Material: Stainless steel
- Country of origin: EU
- Productivity: 800 psc/h
- Material: Stainless steel
- Operation mode: Semi-automatic
CIP-201 - installation for cleaning and disinfection of vessels and pipelines in breweries and other food industries with one tank of 200 liters.
- Material: Stainless steel
- Engine power, kW: 0,75
- Voltage: 380-400V
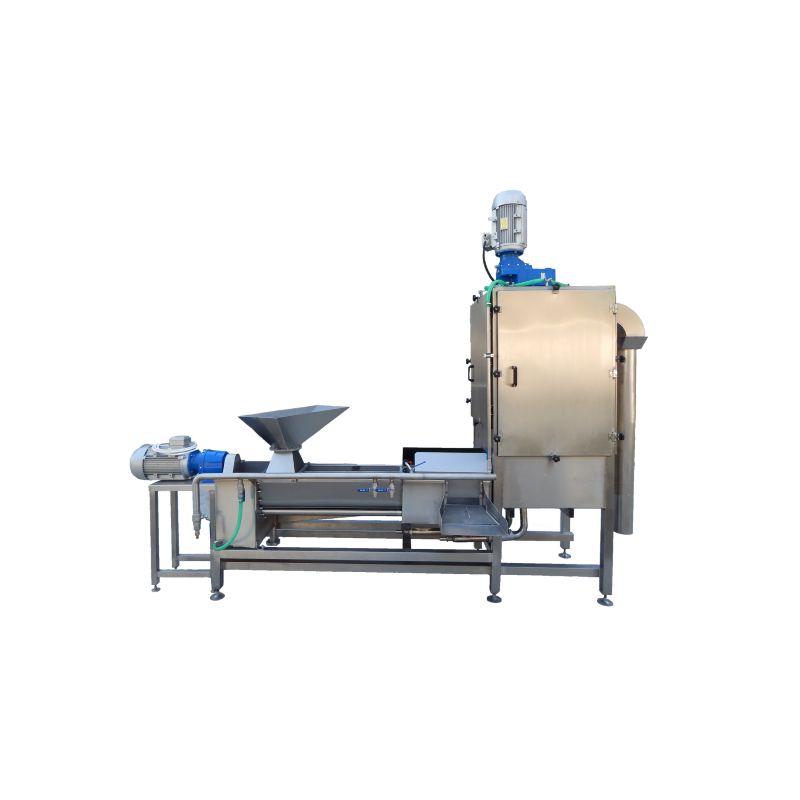
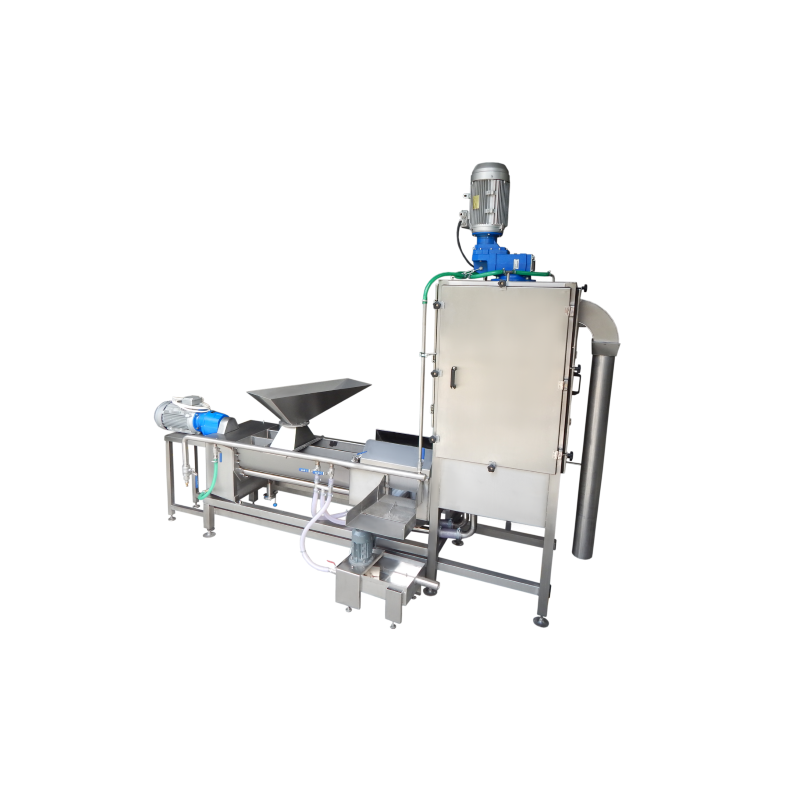
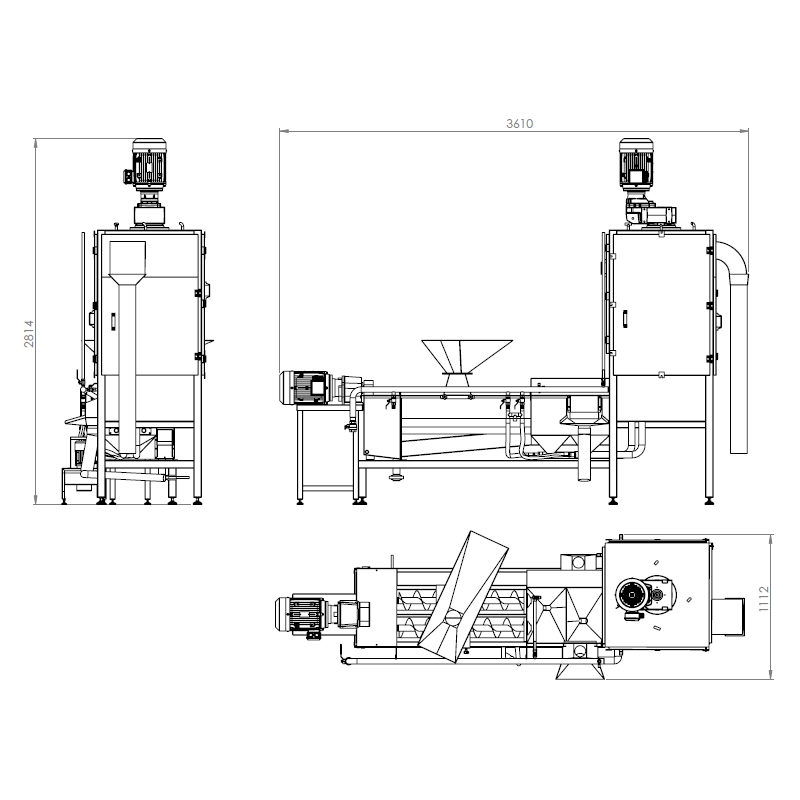
